Efficient & smart end heating
SET | SMART END TREATMENT
Why heat ends?
After quenching and tempering, the stabilizer ends must be closed and hot formed. For this purpose, the ends are heated to a forming temperature of 1000 °C, pressed and quenched. For this purpose, ThermProTEC has developed a flexible system with which both ends are simultaneously fed to a heating device. The variant described here includes fully automatic handling and automated format setting and geometry adjustment.
Procedure
The stabilizers are inserted by a robot into a loading portal with a double gripper system. The loading gantry can accommodate two stabilizers at the same time, alternating between one station for loading and one for thermal treatment. This loading system also serves for manual loading of the stabilizers for sample production. The 2-axis portal positions the stabilizer ends above the induction coils. The actual heating takes place by means of induction, whereby a central generator serves two independently controllable heating circuits. An additional centring gripper is used for precise centring. For heating, the induction coils are pneumatically positioned vertically above the ends and the heating process is started. After completion of the process, the coils are lowered again and two integrated precision pyrometers determine the temperature curve of the component. The data is fed into a database and stored for quality assurance purposes.
Range of services
For the positioning of the induction coils, both sides can be moved individually with servomotors with absolute encoders. The angle of attack is also set in the same way. This means that a format change can be carried out automatically in just a few seconds. The induction coils are designed in a quick-change design so that they can be quickly adapted to special geometries. However, all typical geometries are already covered in the basic equipment. The entire system is of compact design and integrated into a central welded construction. Only the separate cooling unit has to be connected for installation. Operator safety is guaranteed by two integrated safety area scanners. The swivelling control panel can be mounted on either the left or right side. For the control of all pneumatic units, a central mounting panel is provided at the rear. The heating processes for the left and right side can be set independently of each other or the heating can also only be carried out on one side. The system is available in different versions or with heating on one side only. In addition to end forging, these systems can also be used for precise bending of the ends.
You are interested, have questions or suggestions?
Our team is at your disposal. We look forward to your message!
Zunftstr. 20 | 77694 Kehl-Marlen | DE
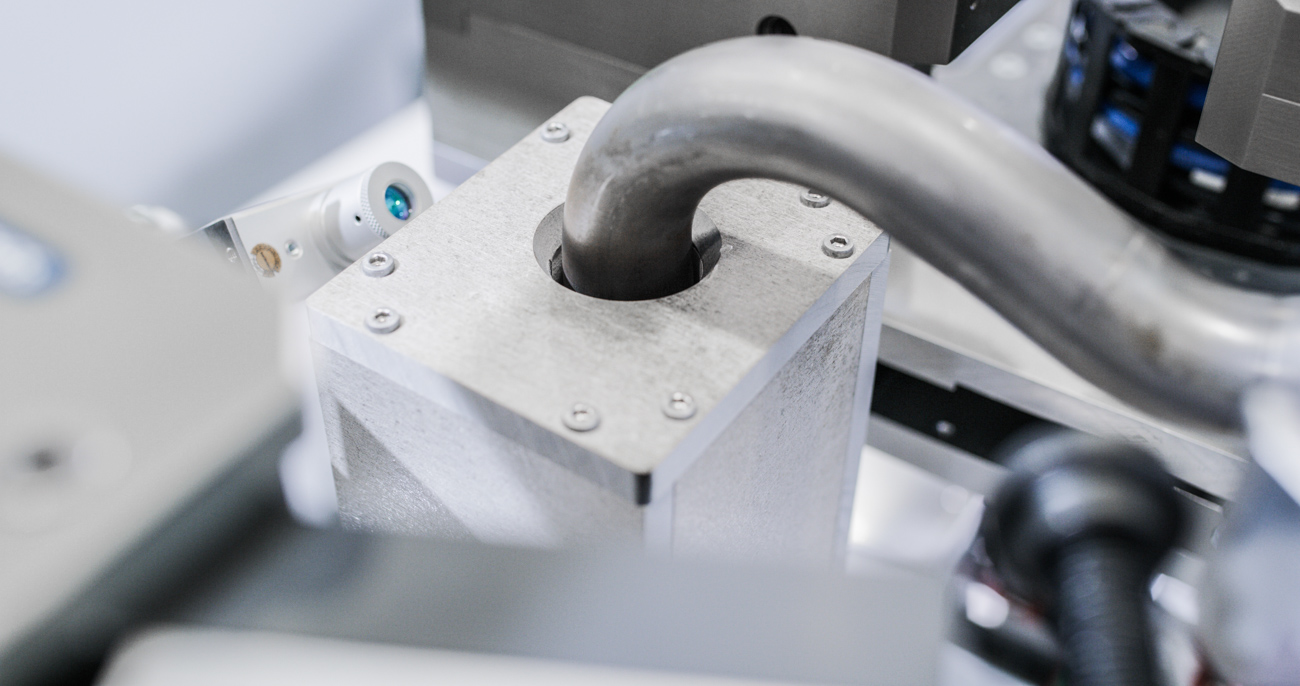
Related products:
Useful links
Contact