Schlüsselfertige Linien für die Stabilisatoren-Fertigung
SBL | SMART BONDING LINE
Wozu eine modulare Fertigungslinie?
Der Markt für Fahrzeugstabilisatoren hat sich in den letzten Jahren signifikant gewandelt. Zum einen kommen aufgrund der heutigen Gewichtsanforderungen anstatt Stabilisatoren aus Vollmaterial Rohrstabilisatoren zum Einsatz. Zum anderen werden diese Bauteile in die geometrischen Randbedingungen eingepasst und in die Karosserie integriert. Dadurch haben sich auch die Befestigungsmöglichkeiten verändert und Gummilager werden auf die Stabilisatoren aufgeklebt. Dabei werden diese mit speziellen Befestigungsschellen verbunden. Gleichzeitig wurden beim Herstellungsprozess energieaufwändige Heißluftöfen durch lokale induktive Erwärmung ersetzt. Dadurch sind deutlich wirtschaftlichere Prozesse realisierbar. Um diesen vielseitigen Anforderungen gerecht zu werden hat die ThermProTEC ein modulares Fertigungslinienkonzept entwickelt, welches das vollautomatische Herstellen von Stabilisatoren mit allen erdenklichen Qualitätssicherungssystemen umsetzt.
Module der Fertigungslinie
Herzstück der Linie bildet ein neues Werkstückträgerkonzept mit dessen Hilfe Haftlager auf einem Staurollenfördersystem durch Beladung, induktive Erwärmung und Entladung gefördert werden. Die Basiskomponenten Transportband, vollautomatisches Beladesystem, induktives Beheizsystem und Entladesystem sind feste Bestandteile der Einheit. Je nach gewünschtem Automatisierungsgrad können auf der Beladeseite die automatische Stabzuführung, Durchmesser- und Gewichtsmessung, Aufbringen des Barcodes, Beflämmen, Bürsten und Ölen sowie das Entfernen von Sicherungsschrauben vollautomatisch mit Robotersystemen erweitert werden. Auf der Entladeseite wird die Befestigungsschelle mittels einer Presse mit automatischer Schellenzuführung sowie die nachfolgende Qualitätssicherung mit Kamerasystemen und Roboterhandling integriert. Die Anlage ist für unterschiedliche Zykluszeiten verfügbar. Die kürzesten Zykluszeiten entsprechend einer Kapazität von 240 Stabilisatoren pro Stunde. Formatanpassungen sind vollautomatisch mittels elektrischer Stellantriebe realisiert. Sämtliche Qualitätssicherungssysteme inkl. Poka Yoke sind bei der Systemauslegung möglich und von den Automobilherstellern akzeptiert. Alle Prozessdaten und Eigenschaften des Stabilisators werden in eine Datenbank übertragen und individuell jedem Stabilisator zugeordnet. Dadurch ist eine Rückverfolgbarkeit gewährleistet.
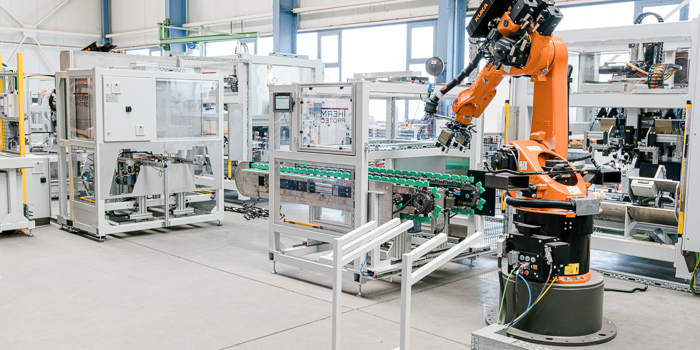
Verwandte Produkte:
Zuführband
Über das zentrale Zuführband werden die Stabilisatoren in die Anlage eingelegt. Der Bediener bestückt das Band manuell mit Stabilisatoren. Die Orientierung wird mittels Sensoren abgefragt. Anschließend ermitteln Präzisionsmesssysteme Durchmesser und Gewicht eines jeden Stabilisators. Bestandteil dieser Einheit ist ein Labelprinter mit Applikator zur individuellen Kennzeichnung der Bauteile. Zur weiteren sicheren Übergabe wird das Bauteil zentriert und an den Handlingsroboter übergeben. Der Barcode wird gelesen und dient zur Identifikation des Bauteils.
Reinigungsstation
Um im späteren Prozess eine sichere Haftung zu gewährleisten muss die Haftstelle vorbehandelt werden. Hierzu dient die zentrale Reinigungsstation. Diese ist mit einer Beflämmeinheit, einer Bürsteneinheit und einer Beölungsstation bestückt. Je nach Anwendung können die einzelnen Arbeitsschritte oder auch eine Kombination aus diesen Schritten durchgeführt werden. Die korrekte Ausführung wird in einer Datenbank protokolliert.
Beladestation
Zentral wichtig für die Qualität des Bauteils ist die Positionierung des Stabilisators in den mit Haftlagern bestückten Werkzeugen. Die Beladestation besteht aus einer nochmaligen präzisen Ausrichtung und Winkelpostionierung und einem 3-Achsbeladesystem, welches den Stabilisator in den Werkstückträgern positioniert. Die Haftlager werden ebenfalls in dieser Einheit mit den Werkzeugen in dieser Position geklemmt und für den weiteren Prozess freigegeben. Hierbei kann die Anpasskraft gezielt eingestellt werden. Das Einstellen des Haftlagerabstandes erfolgt mittels vier Stellmotoren mit Absolutwertgebern. Die Fixierung der Werkstückträger wird über Zentrierpins gewährleistet. In einer manuellen Ausführungsvariante kann hier auch eine zusätzliche Barcodeabfrage integriert werden.
Induktive Erwärmstation
Unser eigens hierfür entwickeltes Induktionssystem (SIU – SMART INDUCTION UNIT) ermöglicht das thermische Verkleben in wenigen Sekunden. Die Erwärmung erfolgt dabei nur lokal im Bereich der Haftlager und ist dadurch äußerst energieeffizient. Je nach gewünschter Taktzeit und Haftlagergeometrie werden ein oder zwei Induktionsstationen in den Prozess integriert. Die Qualitätssicherung erfolgt durch Ermittlung der Temperatur der Haftlagerstellen mit Pyrometern sowie der Messung der tatsächlich benötigten Energie. Für die finale Haftqualität ist die Nachwärmzeit entscheidend. Diese wird durch die Taktung des weiteren Verlaufs des Bandes sichergestellt.peichert.
Schellenzuführung
Zur automatischen Schellenzuführung und damit auch zur Reduktion der Taktzeit ist optional ein Schellenzuführband mit ein bis zwei Handlingsrobotern verfügbar. Diese entnehmen nach einer Kameraüberwachung die Schellen von einem Transportband und bestücken damit automatisch die Presswerkzeuge. Für einteilige Schellen genügt dafür ein einfaches Transportband. Zwei- bzw. vierteilige Schellen werden mit einem doppelten Transportband zugeführt. Die Zuführung der Schellen sowie die Bestückung der Schellencrimpmuttern kann ebenfalls automatisch erfolgen. Für die Schellen wird hierbei ein kameragestütztes “Pick and Place” – System verwendet.
Presse
Die Schellen werden mit einer hydraulisch/-pneumatischen Presse auf den Stabilisator aufgebracht. Die Aufpresskraft beträgt bis zu 25 t pro Seite und ermöglicht das Aufbringen von ein-, zwei- oder vierteiligen Schellen. Die Einstellung des Schellenabstandes wird mittels eines elektrischen Stellanstriebs mit Absolutwertgebern vorgenommen. Über einen mit Poka Yoke gesicherten Werkzeugwechselssystem werden unterschiedliche Schellentypen integriert. Zusätzliche Sensoren an den Werkzeugen sichern die Qualität der Verpressung. Eine spezielle Variante davon ermöglicht eine Omegapressung, bei der die Schellen aufgezogen und auf ein definiertes Endmass zusammengedrückt werden.
GU-System
Optional kann die Geometrie des Bauteils am Ende der Prozesskette automatisch vermessen und somit das Risiko von Fehlteilen reduziert werden. Zu diesem Zweck führt ein Handlingsroboter den fertigen Stabilisator einem optischen Vermessungssystem zu. Ein pneumatischer Greifer auf einer höhenverstellbaren Servoachse positioniert den Stabilisator vor zwei stationären Kameras. Ein weiterer Roboter mit einer Smartcam vermisst zusätzlich die Befestigungspunkte der Schelle sowie die Ausrichtung des Stabilisators in der Schelle. Nach diesem Prozess wird der Stabilisator einem Ausfuhrband zugeführt und damit aus der sicheren Zelle zur Entnahme transportiert. Auch diese Daten werden der zentralen Datenbank zugeführt und gespeichert.
Entladestation
Die Entladestation ist analog aufgebaut zur Beladestation. Die Werkstückträger werden geöffnet und mit dem 3-Achsbeladeportal einer Haftlagerabstandsmessung zugeführt. Mittels zweier Smartcams wird der Abstand ermittelt und in einer Datenbank dokumentiert. Nach diesem Prozess werden die Stabilisatoren in einer Station bzw. auf ein Übergabeband abgelegt. Lichtschranken sichern den Bereich im Falle eines manuellen Handlings der Anlage. Die Formateinstellung erfolgt hier ebenfalls mit integrierten Stellmotoren mit Absolutwertgebern.
Sie sind interessiert, haben Fragen oder Anregungen?
Unser Team steht Ihnen gerne zur Verfügung. Wir freuen uns auf Ihre Nachricht!
Zunftstr. 20 | 77694 Kehl-Marlen | DE
Von der Prozessentwicklung bis zur schlüsselfertigen Produktionsanlage. Wir entwickeln innovative Lösungen im Bereich der thermischen Prozesstechnik. Von der Automobilindustrie bis hin zum Bergbau sind Sie bei uns gut aufgehoben.
Nützliche Links
Kontakt